Waterproofing the floor in the bathroom under the tiles
According to the SNiP standards, waterproofing the floor in the bathroom should 100% prevent water from leaking to the lower floors of residential buildings. Since the microclimate in the room is very specific and involves high humidity, before making the finishing lining of the base, you should take care of high-quality moisture insulation. In the article we will tell you what materials, as well as methods for finishing floor bases, will be optimal in the case of arranging "damp" rooms.
Floor protection from water
How to make high-quality floor insulation in the bathroom? In the process of carrying out all the necessary work, it is necessary to take into account many technical nuances, on which the period of trouble-free operation of the floor will depend in the future. Waterproofing has only one purpose - high-quality protection of the floor covering from the negative effects of moisture.
According to the rules specified in the SNiP, insulation must be carried out without fail if the room was redevelopment or the old coating was dismantled. Modern materials with a low water absorption coefficient perform several tasks at once:
- prevent water leakage floor finish coating;
- prevent damage and destruction of the base;
- protect the floor from the appearance of fungus and mold;
- prevent the accumulation of condensate under the floor.
If you decide to do the insulation in the bathroom under the tiles with your own hands, but have never encountered such tasks before, be prepared for an early replacement of the cladding. In case of non-compliance with the technological conditions and standards regulated by SNiP, the floor is unlikely to last more than three to four years.
During the implementation of construction works, various methods of waterproofing can be used, the choice of which depends on the following factors:
- condition of the draft base;
- the quality of the materials that make up the floor;
- minimum terms for carrying out insulation work;
- number of storeys of the apartment (above the neighbor's apartment, above the basement);
- potential for ceiling height reduction.
The rather complicated installation of floors involves the use of building skills and knowledge, without which high-quality waterproofing is simply impossible. That is why finishing coatings with your own hands can be fraught with serious consequences. For example, in the process of insulating a floor from wooden floors, bulk materials cannot be used, since they create a large static load on the base. According to SNiP, non-compliance with technological standards may entail administrative liability.
Types of waterproofers for bathrooms
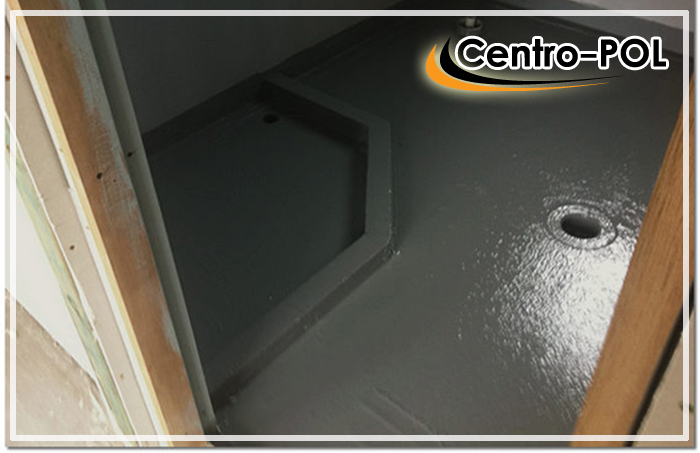
Before proceeding with construction work, it is worthwhile to understand the main types of waterproofers that are used to finish "damp" premises. Consider the existing types of insulation and the materials necessary for this in more detail:
- Sticking. In this case, bitumen-based waterproofing materials are used. They can be both rolled and sheet. The most popular of them include roofing felt, roofing material, polymer and glass steel sheets. When planning the laying of insulators with your own hands, you can choose coatings with various mounting options, namely:
- self-adhesive;
- glued (using special mastic or glue);
- heated (using a gas burner).
- Coating. Liquid waterproofing of the floor in the bathroom is one of the most popular in modern construction. To finish the base, liquid compositions are used, which, after solidification, form a monolithic layer with excellent water-repellent properties. Filling can be done in a cold or hot way, depending on whether the materials are heated before use or not. This method of waterproofing is optimal for arranging a floor for tiles, in which the liquid composition is poured directly onto the concrete screed;
- Coloring. The simplest isolation method that is easy to do with your own hands. However, the insulator will not last as long as we would like - only 3-4 years. Bitumen or polymer varnish with low hygroscopicity is used as a material for work. The method is suitable for finishing the base for tiles, i.e. liquid mastic is applied directly to the screed, as in the previous version;
- Backfill. Bulk materials such as expanded clay are used as a waterproofing agent. But it creates a large load on the floor, so it is suitable for do-it-yourself bathrooms on the first floors of houses;
- Plastering. Thick consistency compositions include polymer additives with good water-repellent parameters. The device of the floor with the help of plaster insulators involves repeated application of the material on the prepared base.
The video clip below will help you learn about the features of waterproofing coatings.
Features of coating (liquid) insulators
For finishing "damp" premises, coating waterproofing and rolled moisture-proof coatings are most often used. The first type of insulator has good adhesion, resistance to temperature extremes and moisture. Therefore, they slowly begin to displace roll and sheet materials.
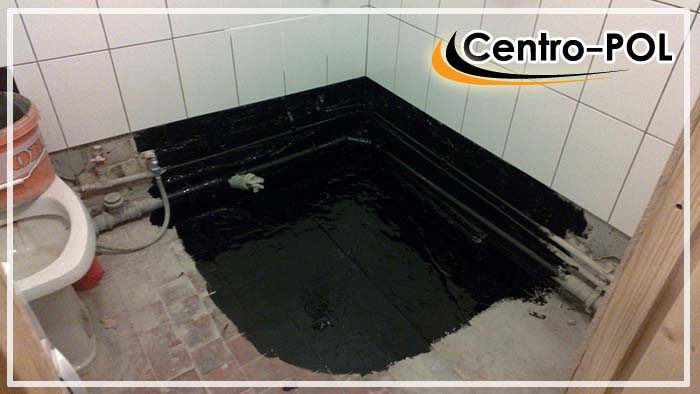
Coating (liquid) waterproofing according to SNiP can be carried out using the following types of coatings:
- Cement-polymer. Universal mixtures with good hydro and thermal insulation. Are applied to carrying out insulating works with a floor, walls and a ceiling;
- Bitumen-polymer. The composition of liquid coatings includes latex fillers, bitumen, plasticizers and organic components. Mastic provides good adhesion to the base and almost 100% protection against moisture;
- Acrylic. Aqueous emulsion materials are more often used for finishing the rough coating for tiles, since they are characterized by high adhesion, strength and water resistance;
- Bituminous. One of the most economical insulator options, suitable for finishing concrete and wood floors. Both "cold" and "hot" bitumen can be used in the process of work. The first is not recommended for use in the case of waterproofing a concrete screed due to the possible contact of alkaline and acidic environments.
For your information. Coating waterproofing is by far one of the most affordable and optimal, since it allows you to form something like a monolithic trough in the room, from which water leakage is almost impossible.
Features of roll and sheet insulators
The base device using roll and sheet coatings is one of the most budgetary. The price of materials varies from 1.5 to 20 dollars per m2. Due to the cost-effectiveness and ease of work, insulators are still in demand among consumers, although objectively these types of coatings are inferior in their technical qualities to liquid formulations.
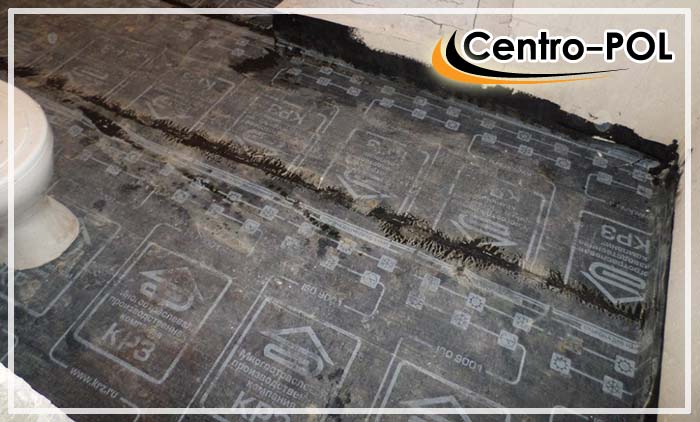
Which insulators are the most in demand?
- only;
- ruberoid;
- glass roofing material;
- diffuse PVC membranes;
- shrink tapes;
- sheet hydrobarriers.
When laying materials with your own hands, you should pay special attention to the processing of the seams between the sheets. Leakage of the coating will lead to leaks, as a result of which fungus and mold can form under the floor, which will lead to the rapid destruction of the base. You can learn more about the process of laying roofing material in the bathroom from the video clip.
Pros and cons of different waterproofing methods
Since liquid and rolled waterproofing agents are in the greatest demand among consumers, we will consider the advantages and disadvantages of each of the waterproofing options:
Coating waterproofers
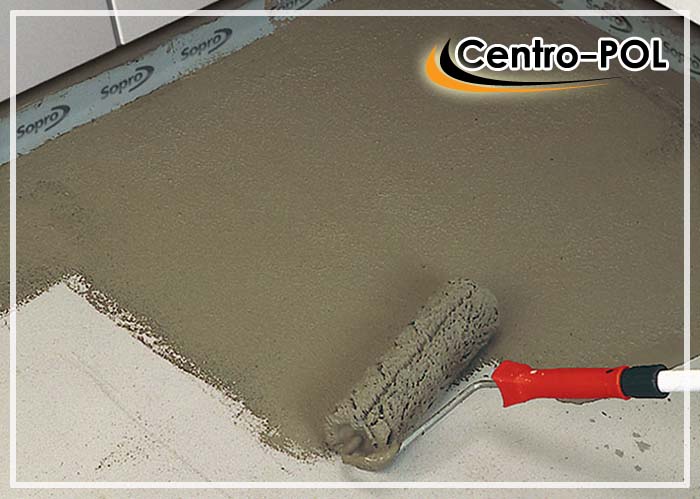
- good adhesion to the rough base;
- the formation of a monolithic waterproof layer;
- resistance to the influence of chemical reagents;
- simple application method;
- relatively low cost of materials;
- toxicity of materials in the liquid state;
- low strength;
- slight frost resistance.
Roll waterproofing
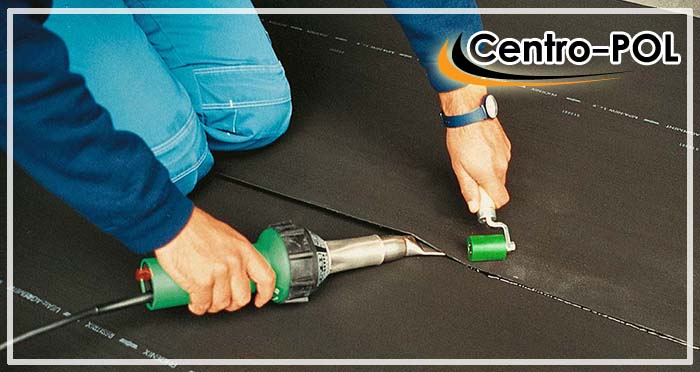
- low cost of roll and sheet coatings;
- simple installation (in case of using self-adhesive films);
- high thermal stability;
- complexity in the process of finishing joints;
- unpleasant odor associated with the presence of bitumen in the composition;
- inability to use in the underfloor heating system.
As already noted, it is very important that the rules provided for in SNiP are taken into account in the process of waterproofing the bathroom. When arranging a bathroom, it is desirable to pay attention to such points:
- In the process of redevelopment of the bathroom, before laying the finish coating, waterproofing must be carried out without fail;
- According to clause 4.11 of SNiP, the floor level in the bathroom should be at least 15 cm lower than in other rooms;
- In accordance with paragraph 2.03 and paragraph 13.89 of SNiP, after combining the bathroom with the toilet or expanding the area of \u200b\u200bthe bathroom, before installing the tiles, it is necessary to make high-quality waterproofing.
Tip: if you are planning to make not just a major overhaul in the bathroom, but redevelopment, before starting work, coordinate the project you have developed with the engineers in the appropriate authorities. Otherwise, the redevelopment will be considered illegal, as a result of which you will incur administrative liability.
Cost of work
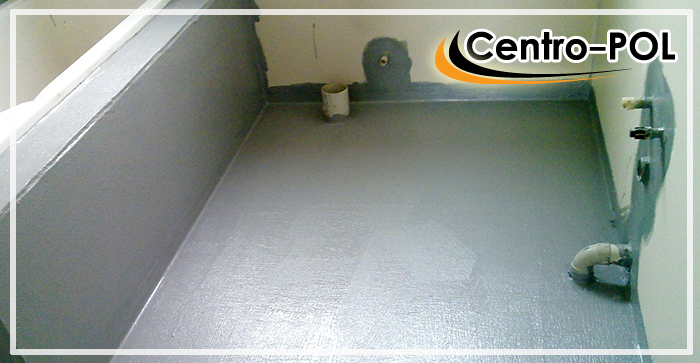
How much does additional waterproofing of a bathroom cost? The cost of the work depends on a large number of factors, namely:
- condition of the subfloor;
- base area;
- type of waterproofing;
- type of materials used;
- complexity of related work.
How much will waterproofing a concrete floor already prepared for tiles cost?
- In the case of using penetrating waterproofing, the price for processing 1 m2 of coating will vary from 3.5 to 5 dollars;
- When finishing the floor with a rolled insulator, the cost of work will be approximately 3-4.5 dollars per m 2;
- Base waterproofing for underfloor heating will be at least $4 per m2.
To understand how much it will cost to fully prepare the base for laying the finish coat (filling the screed, steam, - hydro, - thermal insulation), you should consult with specialists.
Tip: when applying for help to a construction company, give preference only to those companies that have a good reputation and positive reviews from real people.
Overview of the best manufacturers of insulating materials
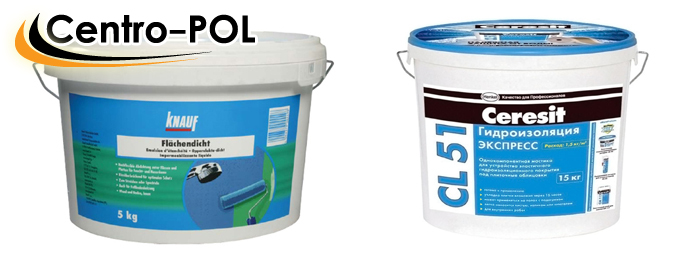
Different types of waterproofers have different technical characteristics and service life. Which of them is better to choose? First of all, you should pay attention to the manufacturer. Among the best manufacturers of insulating materials it is fashionable to include:
Knauf
Knauf is one of the most conscientious manufacturers of waterproofing materials. The Bavarian company specializes in the production of liquid formulations that contain chemically inert fillers and latex components with a low water absorption coefficient. The benefits of Knauf products include:
- Physiological safety and no unpleasant odor;
- High resistance to temperature extremes (from -20 to +60 degrees);
- Waterproof;
- microbiological stability.
ceresite
Ceresit is a Polish company that produces almost all existing types of waterproofing materials:
- mastics;
- film materials;
- hydrophobic liquids;
- polymer mixtures.
The advantages of Ceresit insulators include:
- high adhesion to the base;
- low coefficient of water absorption;